June 2-Sept 29, 2019
** Since doing the first flight I have been doing flight testing and fixing issues. The biggest has been high oil and cylinder temps. On high power climbs and speed runs the cylinder head temps was hitting 465 at the max and the oil temps were going to 245. Those are max temps that I can't have, even when the engine is still breaking in. I worked hard at sealing the engine baffling, which helped, but not enough. I tried relocating the oil cooler to a position that may have more air flow. That didn't work. All my flying is from 7,000' to 11,000'ASL. When the density altitude is considered I just wasn't getting enough pressure in the upper level of the cowl. Time to try something else, so I changed from a 7 row (standard) oil cooler to a 10 row. That helped, but still not enough. Time to increase the inlets. They are 5" diameter standard size. The biggest they can be expanded is to 5 3/4". That is a 32% increase in area. I found a paint bucket that was just the right size to use as a mold. Thank goodness for a fiberglass airplane! The original inlets have a flat face at the entrance. I rounded the new openings, to smooth the airflow. What a difference! All the temps are now staying in the green. They still elevate in a hard climb, but still stay acceptable, and drop quickly when the nose is lowered. I lost a bit of speed but that's a good tradeoff.
** The oil cooler plenum was shaped with a block of foam and a plastic bottle cut to length. several layers of fiberglass laid over the mold, and then the foam & plastic removed after hardening. The shape helps distribute the air evenly over the cooler.
** Found the fuselage belly at the right landing gear warped and cracked. After consulting with Nick it was decided that the brake line feedthrough was squeezing the fiberglass up to the internal metal structure. A relief hole was made in the fuselage so the feedthrough could be tightened up to the metal structure. All is good now.
** The ADS-B was giving me fits. After lots of phoning Garmin, we got the configuration set correctly. After flying in the system and getting the report, it was discovered that there was some pass and some fail. More talking to Garmin and recommending more wire connections, things are working better. It needed to put out a signal that the WAAS is high integrity position source.
** The next problem is the ELT being set off by the 45R transponder. ACK said try wrapping the unit in aluminum foil to block the RF. It worked. Now they need to fix my unit with a new board that will reject the RF. I had a friend with the same problem and ACK changed an internal board that fixed the problem.
** working down through the issues. Next is the trim. There is not enough with full flaps on approach and trim does not trail sufficiently in cruse. Nick is going to check the angle of incidence on his demo plane to compare my wing to horizontal stab.

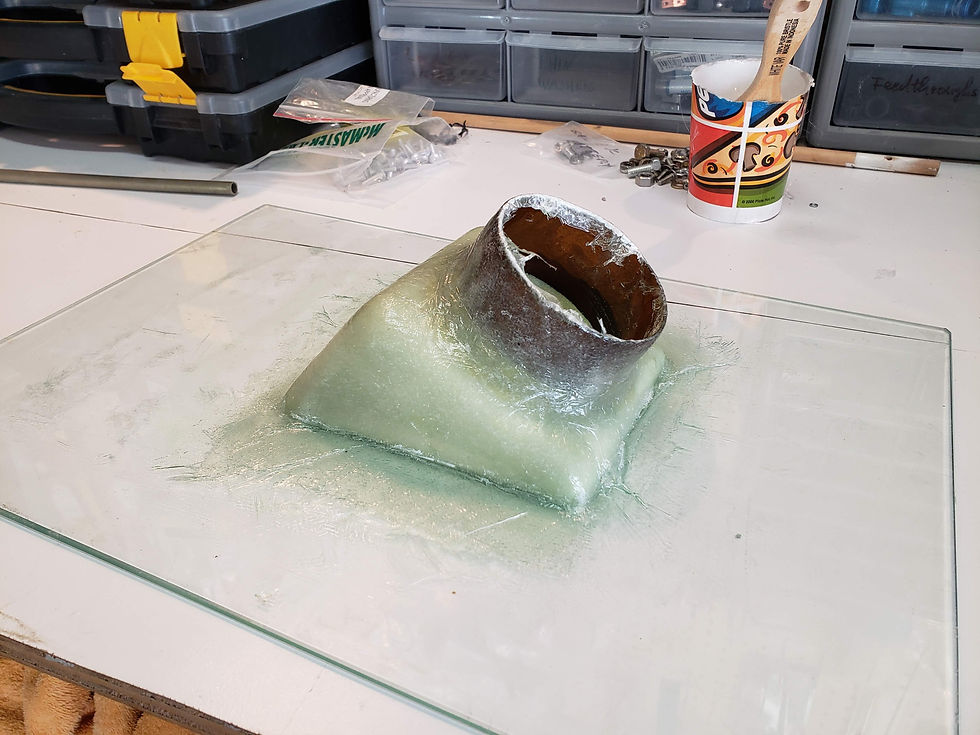
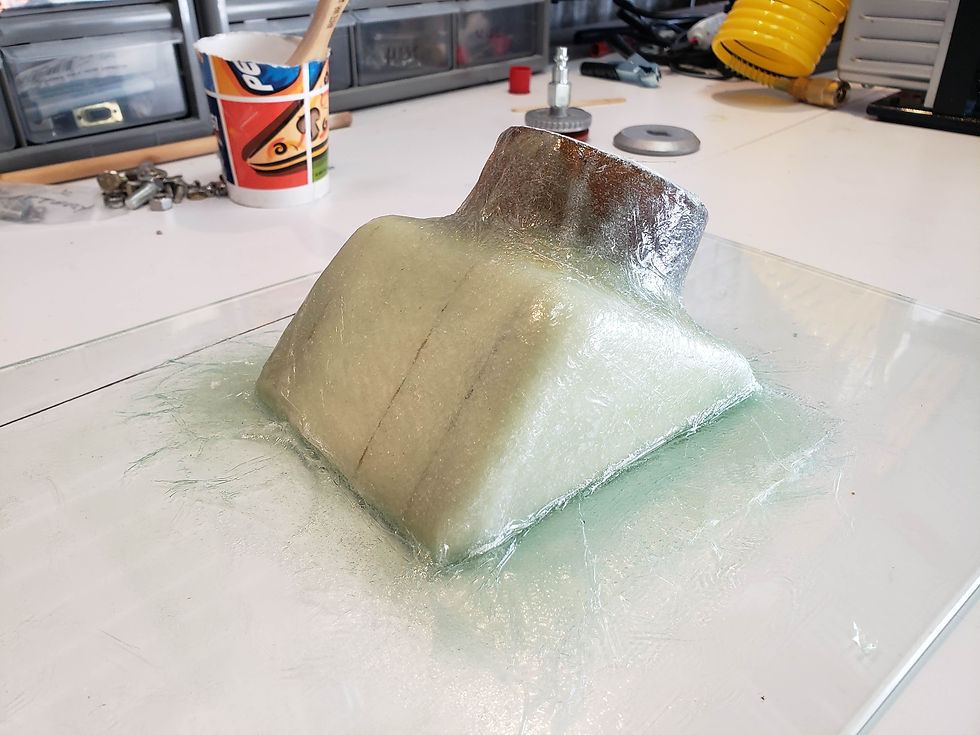

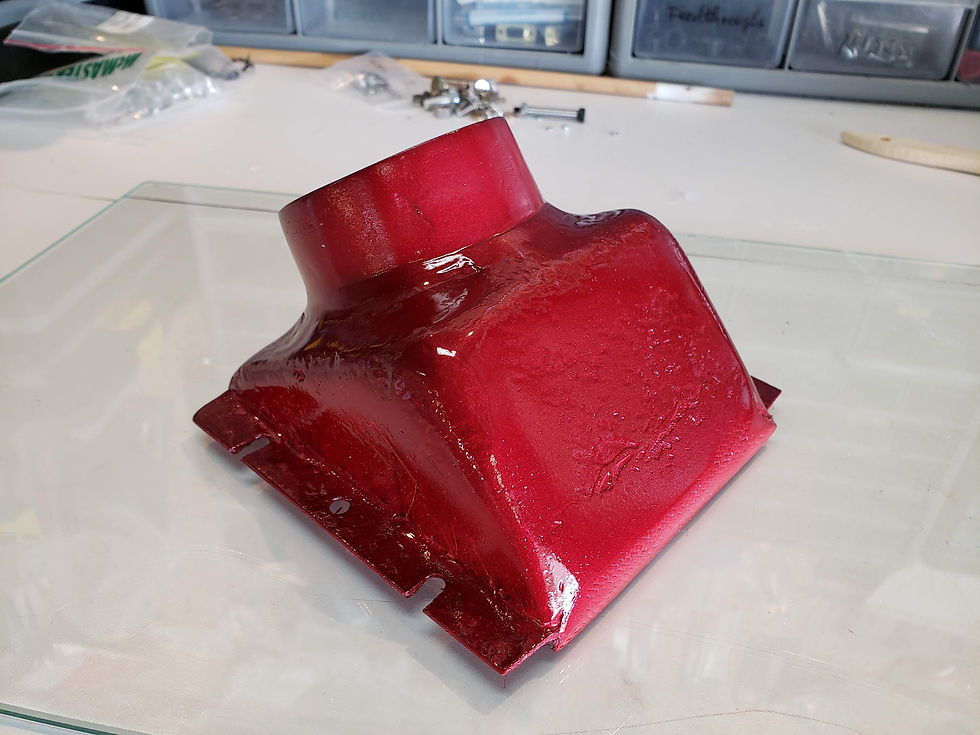
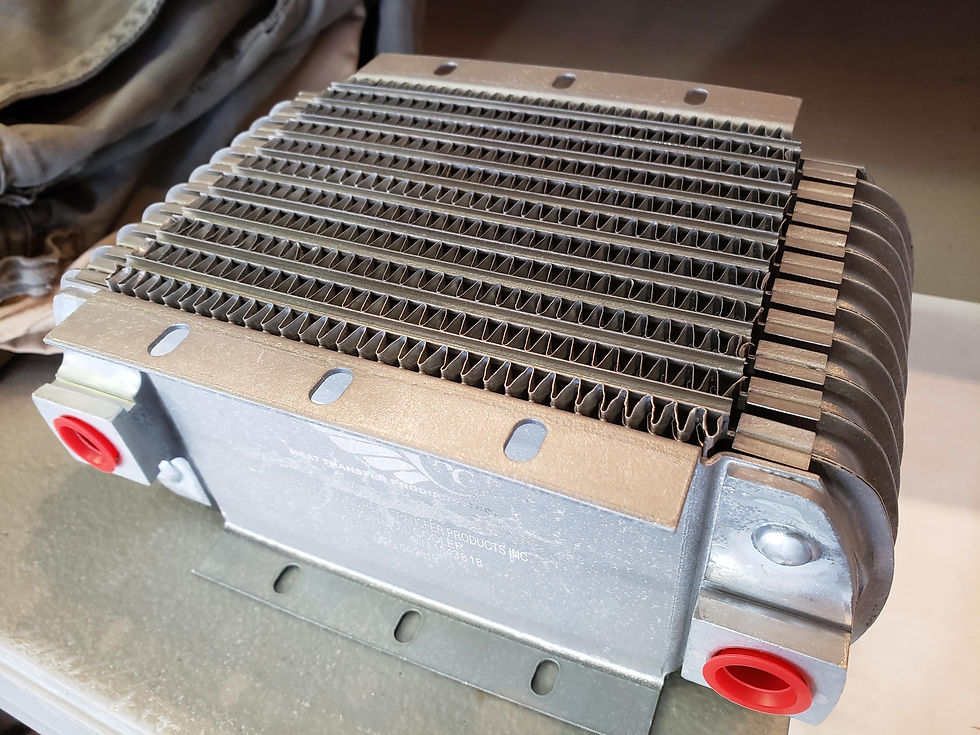
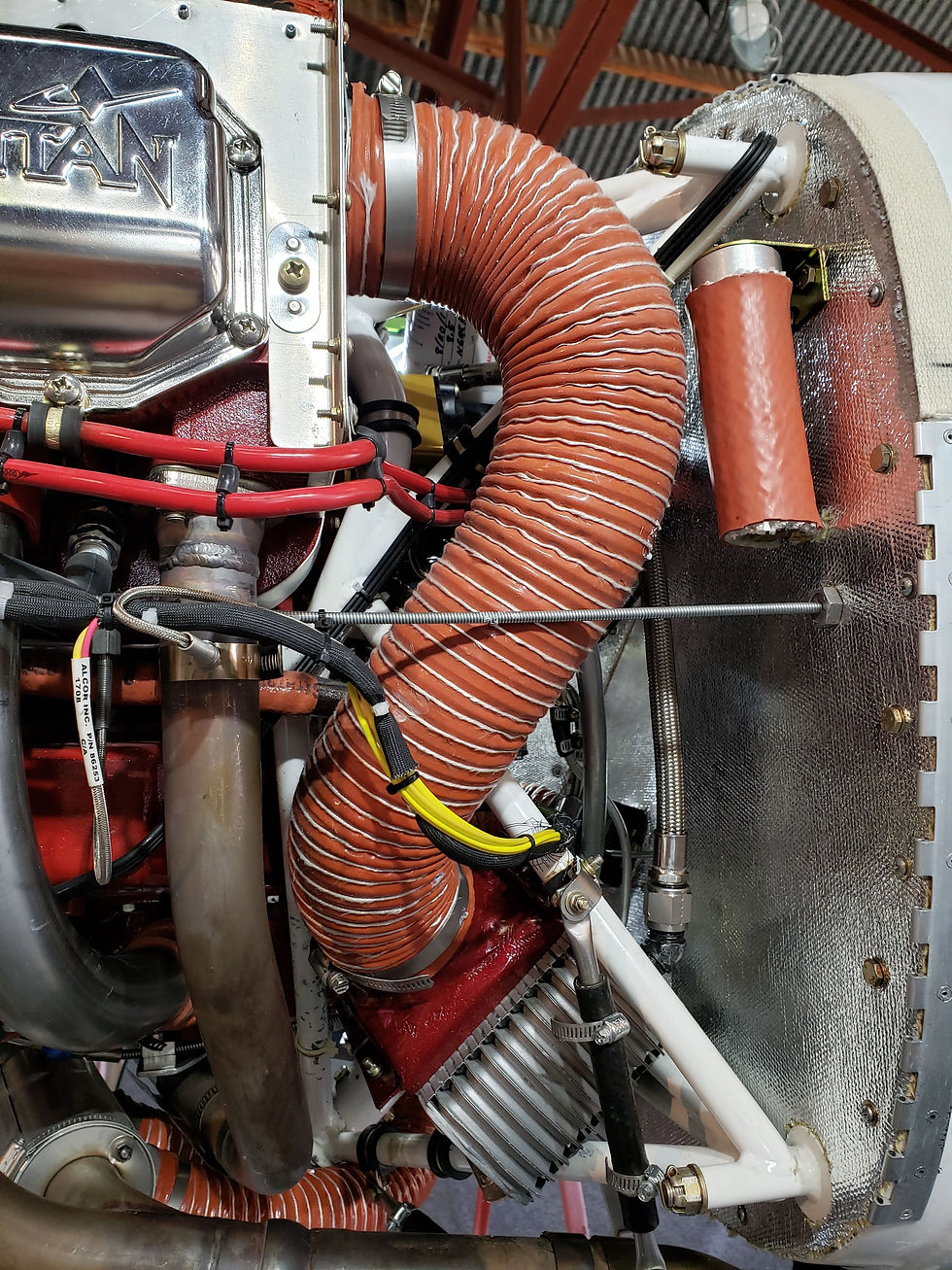
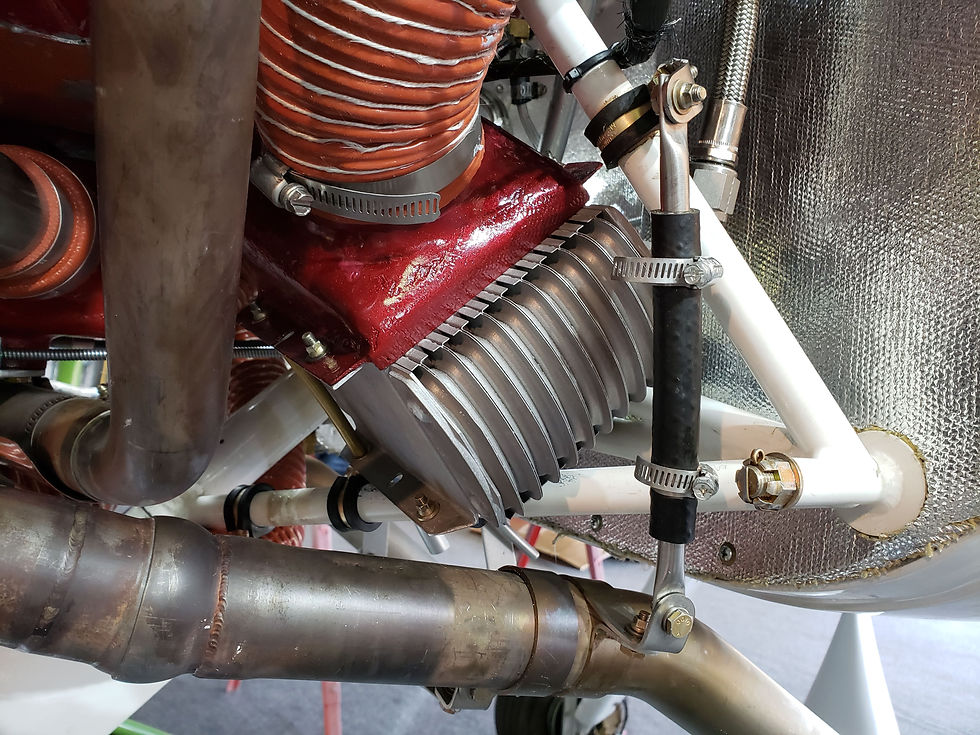
